Concrete readymix
Ready-mixed concrete is produced to order and our staff will be happy to advise you on what concrete class you need if you require help with specification.We can meet any size order, from 0.5m³ to 700m³ continuous pour.
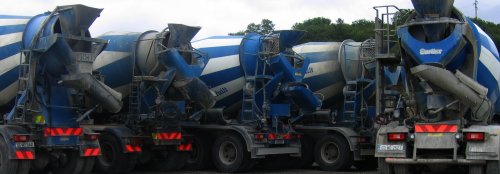
Quality
Quality of product is assured. Molloy Concrete Ltd. is a member of the Irish Concrete Federation and is audited annually by the NSAI. Molloy Concrete Ltd. is approved to supply concrete as per European Standard EN-206-1. (This satisfies the Department of Agriculture requirement for grant approval.)
GGBS
Ground Granulated Blastfurnace Slag (GGBS) cement is a by-product of the steel industry. When melting iron in a blastfurnace a molten slag will form on the top. The slag is mostly silicates (glass) and is the raw material for GGBS cement. The slag is cooled and then finely ground to form GGBS cement.
GGBS cement has exactly the same chemical constituents as ordinary Portland cement (OPC) only in slightly differing proportions. Thus it can replace Portland cement by up to 85% in making ready-mixed concrete. GGBS cement is widely used in concrete in the UK and on the continent for over seventy years. By replacing Portland cement GGBS can reduces the overall CO2, nitrous oxide (NOX) and sulpher dioxide (SO2) emissions in concrete manufacture by half. Correct use of GGBS will extend the life of concrete.
How GGBS cement is used
GGBS cement is added to concrete in the our batching plant, along with Portland cement, aggregates and water. The GGBS replaces Portland cement, on a one- to-one basis by weight- typically 40 to 50%. is used in most instances. GGBS cement is used for
- its environmental benefits
- improved appearance for exposed concrete
- resistance to sulphate and chloride attack
- reduced heat of hydration.
The use of GGBS cement in concrete in Ireland is covered in the new Irish concrete standard IS EN 206-1:2002. This standard establishes two categories of additions to concrete along with ordinary Portland cement: nearly inert additions (Type I) and pozzolanic or latent hydraulic additions (Type II). GGBS cement falls in to the latter category. As GGBS cement is slightly less expensive than Portland cement, concrete made with GGBS cement will be similarly priced to that made with ordinary Portland cement.
Architectural and engineering benefits
Appearance
GGBS cement is a near-white powder. It imparts a lighter, brighter colour to concrete, in contrast to the stoney grey of concrete made with Portland cement. The colour of the finished concrete is lighter, the concrete has a smoother surface finish, and the addition of GGBS to the mix prevents the formation of efflorescence.
The near-white colour of GGBS cement permits architects to achieve a lighter colour for exposed fair-faced concrete finishes, at no extra cost. To achieve a lighter colour finish, GGBS is usually specified at between 50% to 70% replacement levels, although levels as high as 85% can be used. GGBS cement also produces a smoother, more defect free surface, due to the fineness of the GGBS particles. Dirt does not adhere to GGBS concrete as easily as concrete made with Portland cement, reducing maintenance costs. GGBS cement prevents the occurrence of efflorescence, the staining of concrete surfaces by calcium carbonate deposits. Due to its much lower lime content and lower permeability, GGBS is effective in preventing efflorescence when used at replacement levels of 50% to 60%.
Strength
Concrete containing GGBS cement has a higher ultimate strength than concrete made with Portland cement. It has a higher proportion of the strength-enhancing calcium silicate hydrates (CSH) than concrete made with Portland cement only, and a reduced content of free lime, which does not contribute to concrete strength. Concrete made with GGBS continues to gain strength over time, and has been shown to double its 28 day strength over periods of 10 to 12 years (1).
Credits
The information on GGBS presented here is a summary of the excellent article Sustainable Cement, The Eco Friendly, Durable, Low Energy Alternative to OPC on the Construct Ireland website.